ステンレス部品を樹脂部品にリプレイス。
軽量化による現場作業者の負荷軽減、コスト低減を実現。
業務用加湿器のOEMメーカーとして、年間で約5,000台を量産。
業務用加湿器の大手メーカーとのパートナーシップのもと、OEMメーカーとして量産を担う日東。
板金・プレス部品、樹脂成形部品の製造、電子部品の調達、最終組立から出荷までを一貫して担当しています。
業務用加湿器の市場は広く、オフィスビル、学校、病院など多数の施設に設置されています。
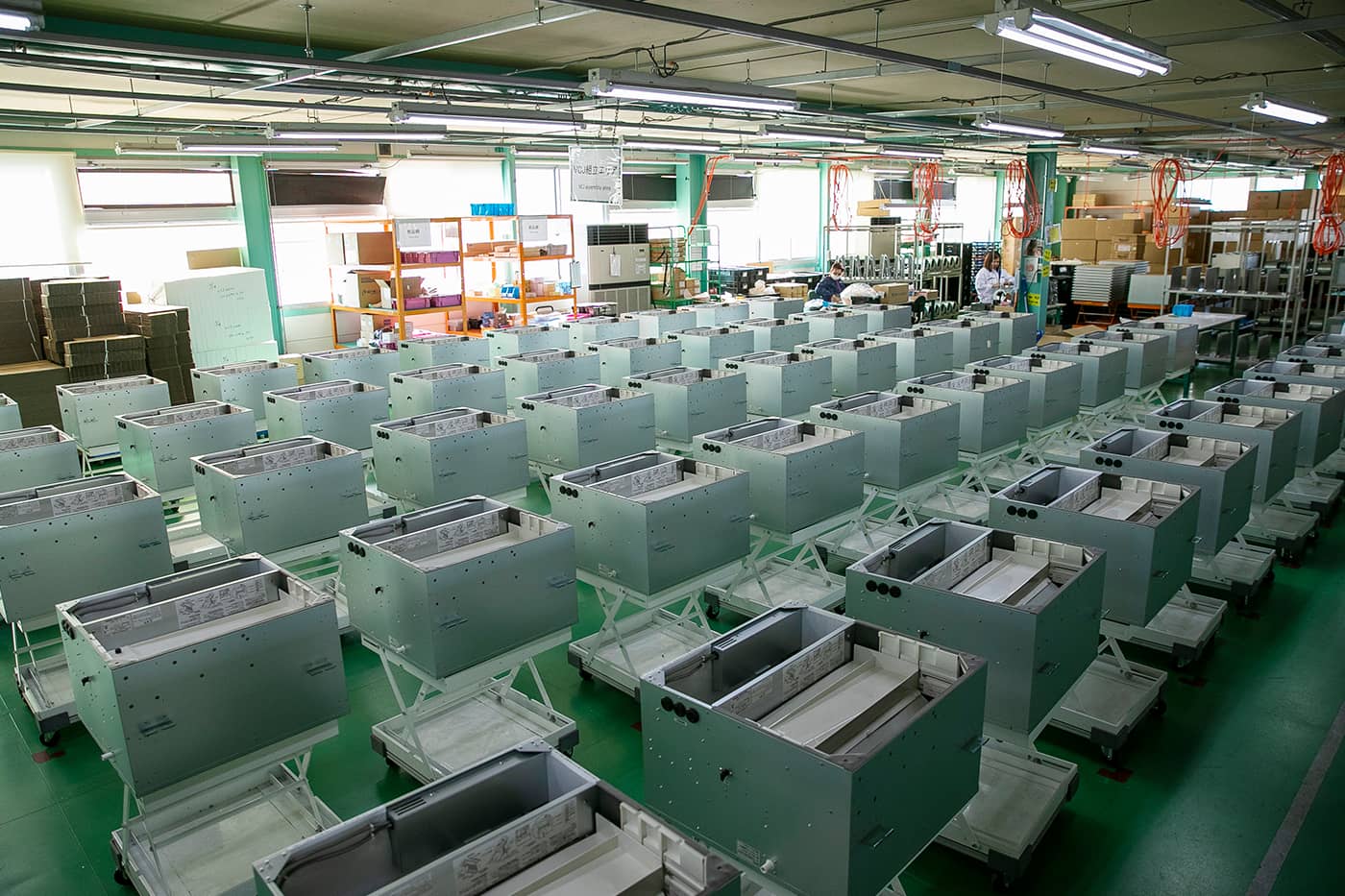
軽量化とコスト低減という大きな課題。
日東が量産・出荷のフェーズを担当し、メーカー様が販売・設置・稼動後のメンテナンスを行う中で、二つの大きな課題が表面化しました。
一つは、製品重量です。設置作業やその後のメンテナンスを行うメーカー様の現場エンジニアにとって製品重量が作業時の負担となっており、なんとか軽量化を測れないかという声が現場から上がっていたのです。
二つ目が、コスト低減です。良質な製品・サービスを市場に供給し続けるため、メーカー様にとってコスト低減は必須課題です。
以上の二つの観点から、日東にも改善のアイデアが求められていました。
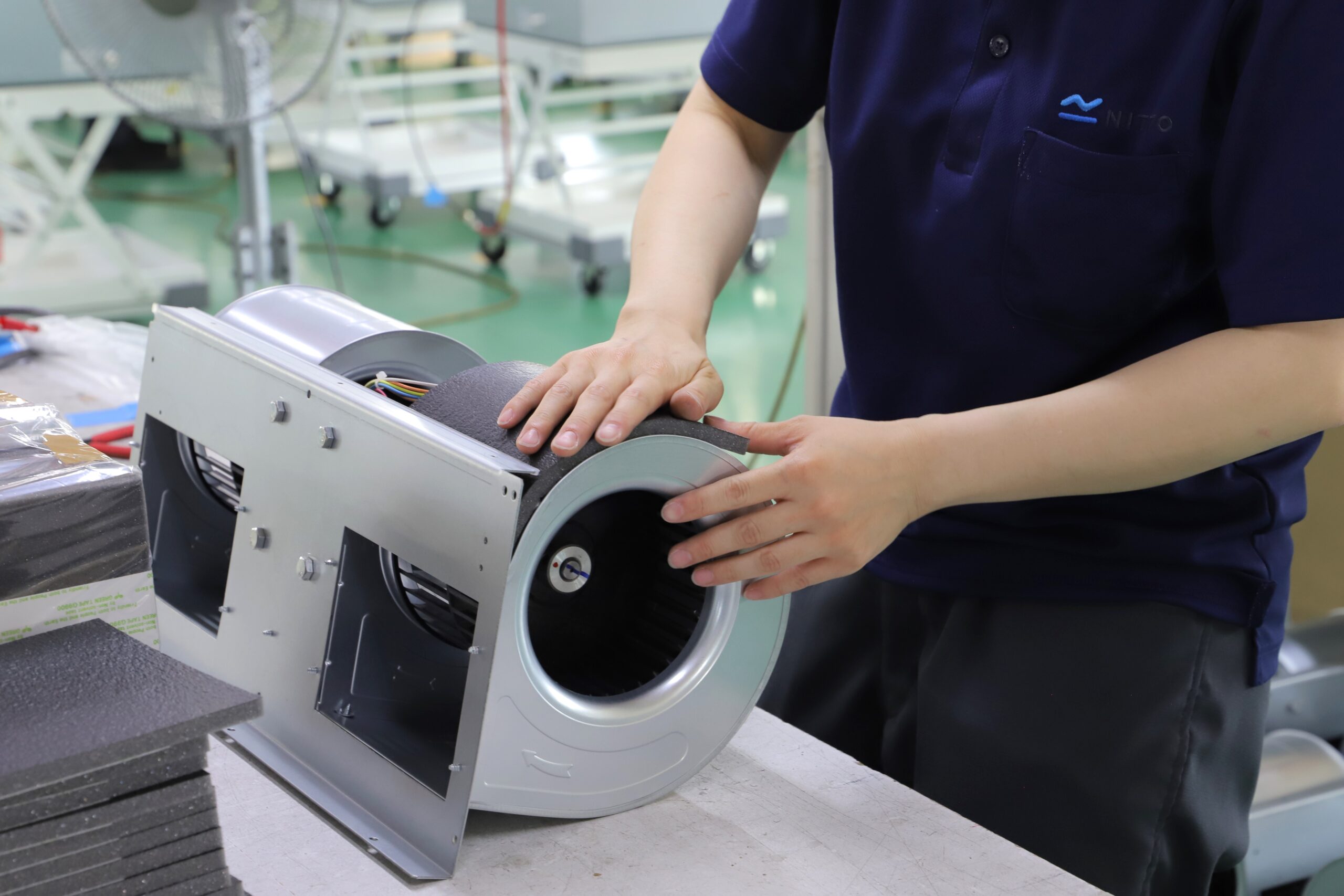
ステンレス部品を樹脂製品にリプレイスするという発想の転換。
課題を念頭に日東の担当者が製品構造の分析にあたったところ、一つの結論にたどり着きました。それは、内部の機構部品の一つをステンレス製から樹脂製に変更するという方法です。
樹脂はステンレスよりも軽量であるため重量を軽減できます。また、長期的な目線では樹脂製のほうがコスト低減につながります。こうした利点を担当者からメーカー様へご提案したところ、実施が決定しました。
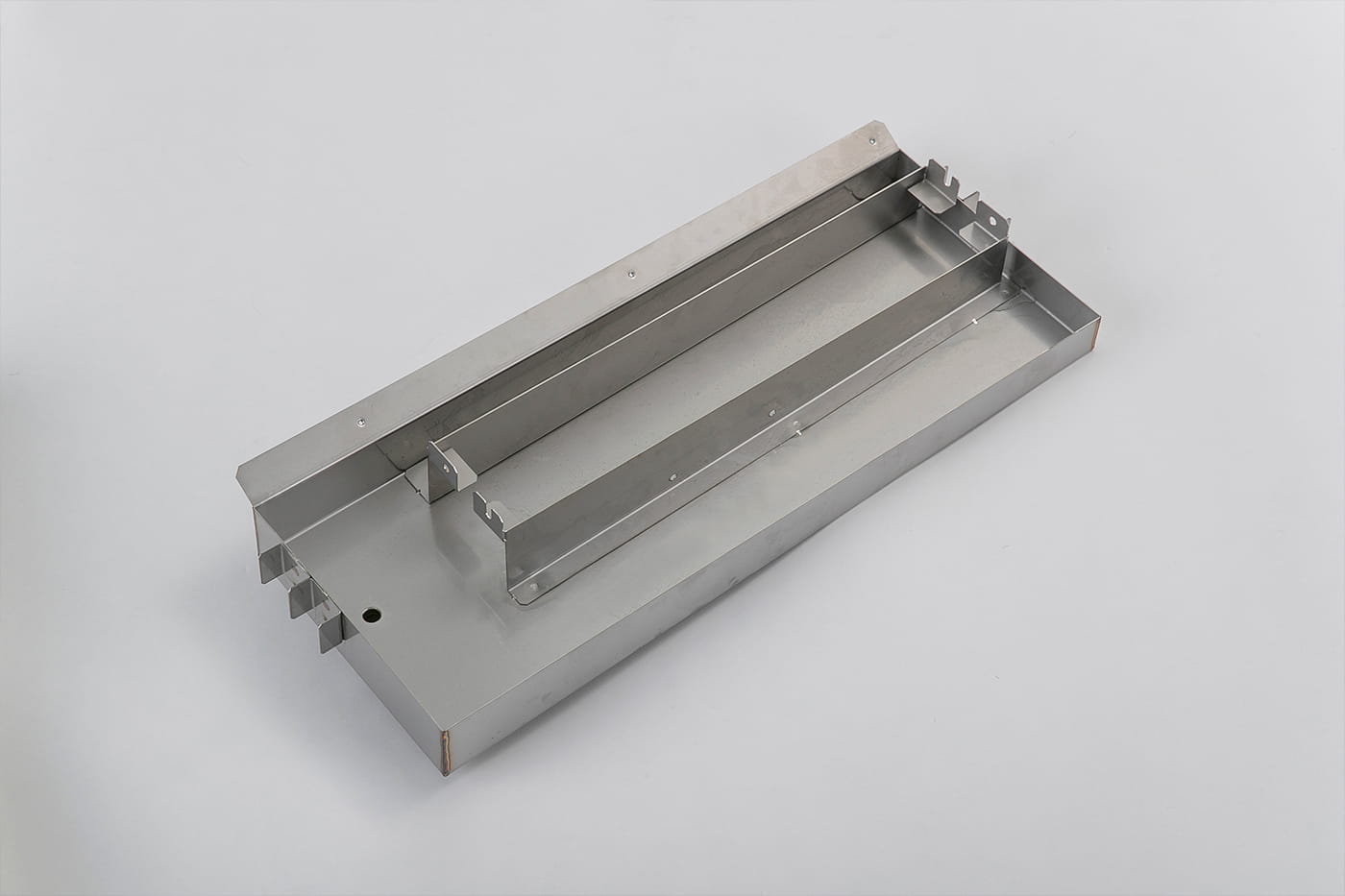
日東のものづくりノウハウ
条件を満たす素材選定ノウハウ。機構設計から改善できるものづくりスキル。
今回、変更を検討したのは「ドレンパン」という部品です。加湿器の中で発生する水分を受け止めて貯水部まで流し込む、いわば雨どいの役割をする部品です。製品内部に占める面積も重量も大きな部品のため樹脂製にリプレイスできれば重量・コストの点で大きな改善が見込めます。
しかし、ひと口に「部品を樹脂製にリプレイスする」と言っても簡単ではありません。問題の一つは材質でした。ステンレスはカビなどの繁殖に強い材料であり、水回りの使用に適しています。樹脂で同等の条件を満たす素材の選定には慎重な検討が必要です。この点で日東には、様々なものづくりにおいて樹脂部品を製造してきたノウハウの蓄積があり、樹脂素材に精通しています。社内の知見から、今回のケースにおいても最適な素材を選定することができました。
もう一つの大きな問題は、材料の強度にありました。樹脂はステンレスに比べて強度が劣るために、固定方法の変更など周囲の機構を改修する必要があったのです。そのため、製品の機構設計から検討を行い、メーカー様との充分な協議のもと製品の改善にあたりました。
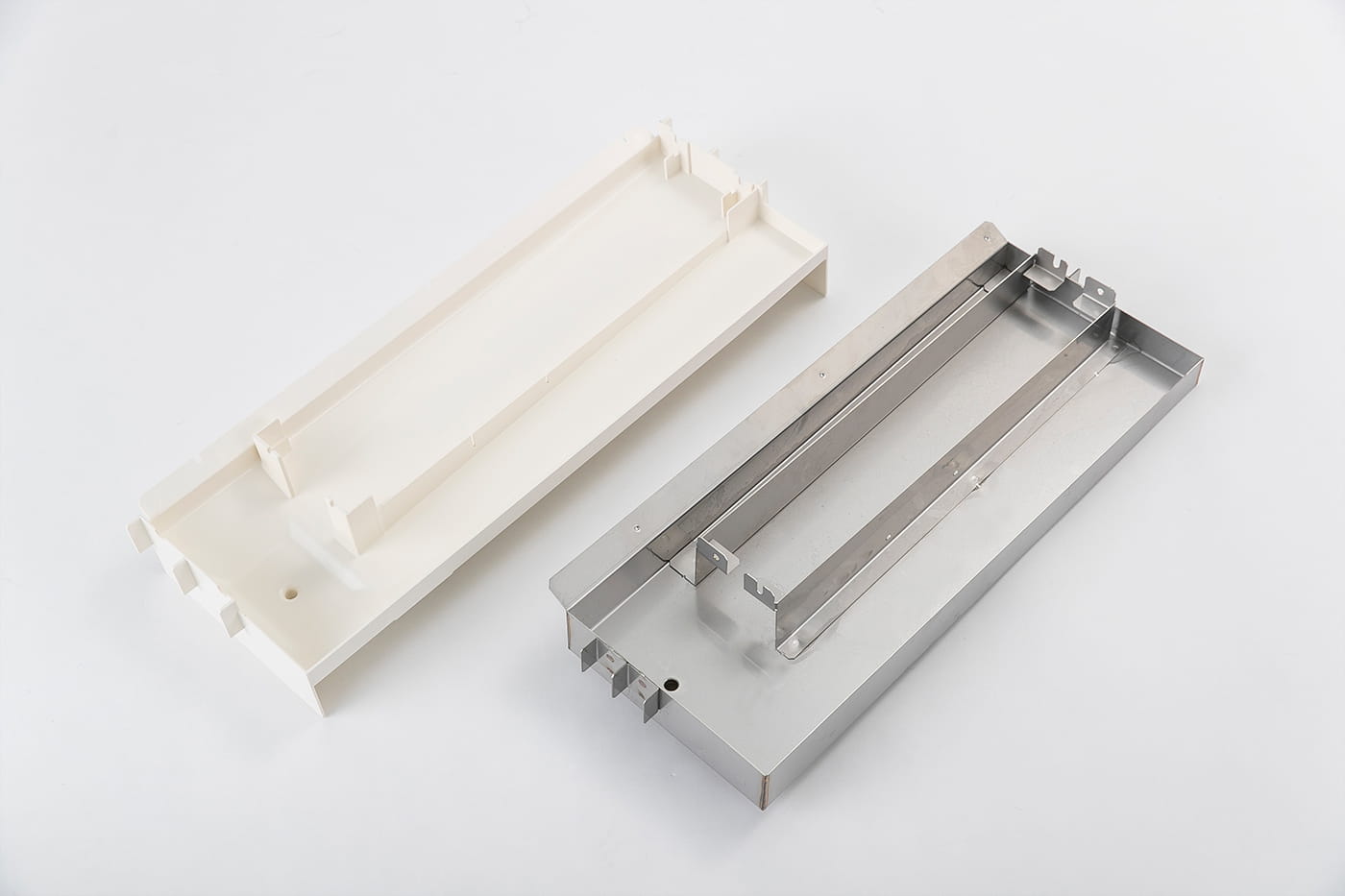
現場エンジニアから「作業が楽になった」との声が届いた。
こうした改善活動の結果、新たな材質と構造を持った製品を無事に市場へ送り出すことができました。
現場のエンジニアからは「軽量化されて作業が楽になった」という声が届きました。また、樹脂製にすることでコスト低減にも成功しました。この点、樹脂部品の成形には金型が必須なために初期投資が必要でしたが、長期的な目線では充分にコスト低減が可能です。また、製造時の工数削減にも寄与したため、リードタイム短縮にもつながっています。
こんなことにお困りならぜひご相談ください
- 板金、プレス部品や樹脂部品のコスト低減を検討したい。
- 板金、プレス部品や樹脂部品の製造工数を削減したい。
- 製品を安定供給するにあたって、開発から改善活動までともに取り組めるパートナーを探している。
- 量産フェーズを任せられる、信頼できるOEMメーカーを探している。